怀化石墨增碳剂厂家 青岛腾瑞炭素有限公司
浏览次数:213次
- 产品规格:
- 发货地:河北省邯郸临漳县
关键词
怀化石墨增碳剂厂家
详细说明
⑴促进石墨化的工艺措施是减少铁液收缩的好措施。
电炉熔炼:增碳技术的应用是解决铁液收缩的关键技术。由于铁液凝固过程中的石墨析出产生石墨化膨胀作用,良好的石墨化会减少铁液的收缩倾向,因此,增碳技术是好的工艺。
由于加入增碳剂提高了铁液的石墨化能力,因此,采用全废钢熔炼加增碳剂的工艺,铁液的收缩倾向反而更小。这是非常重要的一个观念转变,传统的观念是认为多加废钢会铁液的收缩倾向,这样我们就容易走入一个误区,不愿意多用废钢,而喜欢多用一些生铁。
多用生铁的缺点是:生铁中有许多粗大的过共晶石墨,这种粗大的石墨具有遗传性,如果低温熔炼,粗大的石墨难以消除,粗大的石墨从液态遗传到了固态,使凝固过程中本来由于石墨析出应该产生的膨胀作用削弱,因此使铁液凝固过程中的收缩倾向,粗大的石墨又必然降低了材料的性能。因此,与用废钢增碳工艺相比,大量用生铁的缺点就是:①强度性能低。同样成分做过对比试验,性能低半个排号。②收缩倾向大。同样条件下,比废钢增碳工艺收缩大。
对于电炉熔炼,增碳技术的核心是使用的增碳剂。采用废钢增碳工艺,增碳剂就成为增碳工艺中重要的环节。增碳剂质量的好坏决定了铁液质量的好坏,增碳工艺能否获得好的石墨化效果,减少铁液收缩,主要取决于增碳剂:① 增碳剂一定要选用经过高温石墨化处理的增碳剂。只有经过高温石墨化处理,碳原子才能从原来的无序排列变成片状排列,片状石墨才能成为石墨形核的好核心,促进石墨化。②好的增碳剂含硫都非常低,w(S)小于0.03%是一个重要的指标。
对于冲天炉熔炼:高温熔炼是关键的技术指标,高温熔炼可以有效消除生铁粗大石墨的遗传性。高温熔炼可以提高渗碳率,减少配料中的生铁加入量。以渗碳方式获得的碳活性好,要比多加生铁带来的碳有更好的石墨化作用,反映在铸件上,就是石墨的形态更好,分布更均匀。石墨的形态好,就会提高材料的性能,包括切削性能,而 石墨化效果好,就能减少铁液的收缩倾向。
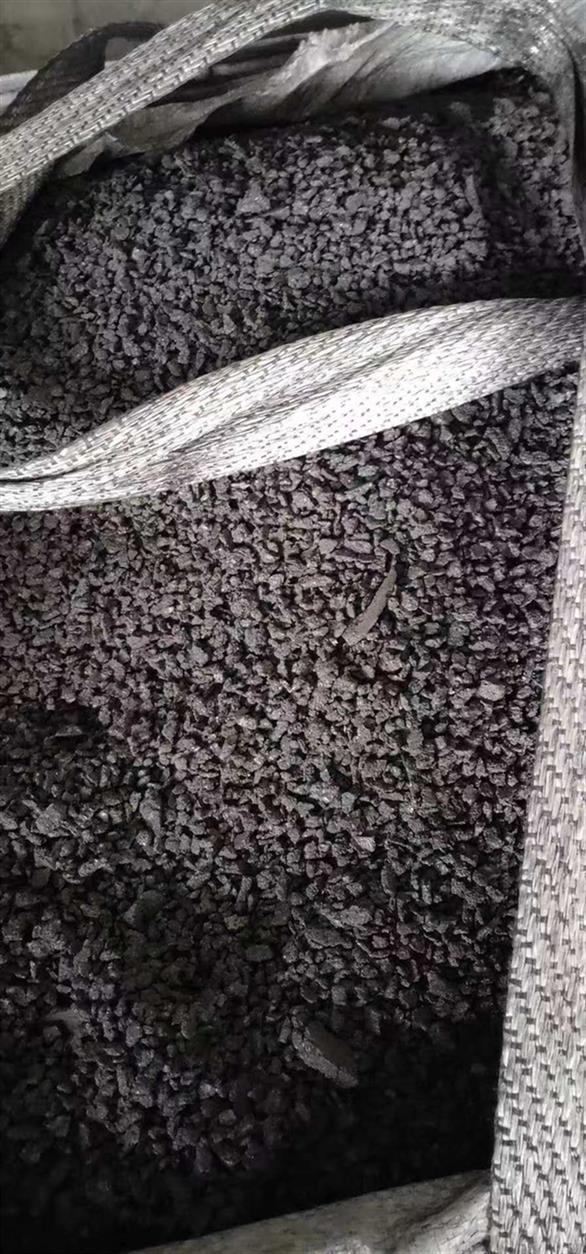
我厂下辖临漳县石峰碳素有限公司和临漳县和峰碳素经销处两家子公司。我厂碳素生产设备完善,技术力量雄厚,检测手段完善,产品质量上乘,品种齐全,主要产品有普通功率石墨电极,高功率石墨电极,特种石墨制品及新型碳素材料等。
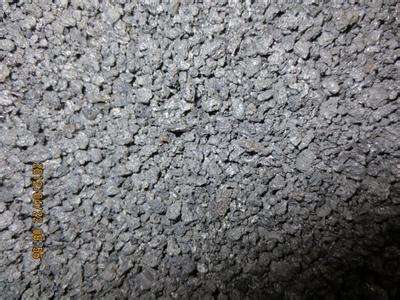
3、铁液化学成分对增碳剂增碳效果的影响
3.1硅对增碳剂增碳效果的影响
铁液中的硅对增碳效果有较大的影响。硅含量高的铁液增碳性不好。有人让铁液中Si的质量分数在0.6%~2.1%的范围内变化,并添加如表1所示的A,B两种增碳剂,观察加入增碳剂后增碳时间的区别,铁液中Si的质量分数高时,增碳速度慢。
3.2硫对增碳剂增碳效果的影响
正如铁液中的硅的质量分数对增碳效果的影响那样,硫的含量对增碳也有一定的影响。用表2中的A增碳剂,在添加前先加入试剂用的硫化铁,观察S的质量分数对增碳的影响。当添加硫化铁、铁液中S的质量分数为0.045%时,将它与无添加硫化铁、铁液中S的质量分数为0.0014%的低硫铁液相比较,增碳速度要迟缓得多。
4、增碳剂选择及加入方法
4.1应选择含氮量少的增碳剂
铸铁铁液中通常的氮的质量分数在100 ppm以下。如果含氮量超过此浓度(150-200 ppm或者更高),易使铸件产生龟裂、缩松或疏松缺陷,厚壁铸件更容易产生。这是由于废钢配比增加时,要加大增碳剂的加入量引起的。焦炭系增碳剂,特别是沥青焦含有大量的氮。电极石墨的氮的质量分数在0.1%以下或极微量,而沥青焦氮的质量分数约为0.6%。如果加入质量分数为0.6%氮的增碳剂2%,仅此就增加了120 ppm质量分数的氮。多量的氮不仅容易产生铸造缺陷,而且氮可以促使珠光体致密、铁素体硬化,强烈提高强度。
4.2增碳剂的加入方法
铁液的搅拌可以促进增碳,因此搅拌力弱的中频感应电炉与搅拌力强的工频感应电炉比较,增碳相对困难得多,所以中频感应电炉有增碳跟不上金属炉料的熔解速度的可能性。
即使是搅拌力强的工频感应电炉,增碳操作也不能忽视。这是因为,从感应电炉熔炼的原理图可知,感应电炉内存在开的搅拌铁流,在其边界的炉壁附近还存在着死角。在炉壁停留、附着的石墨团如果不用过度升温和长时间的铁液保温是不能熔入铁液的。铁液过度升温和长时间的保温,会铁液过冷度,有加大铸铁白口化的倾向。此外,对于在炉壁附近产生强感应电流的中频感应电炉来说,如果附着在炉壁的石墨团之间钻进铁液,在进行下一炉熔炼时,钻进的金属被熔化,导致侵蚀和损伤炉壁。因此,在废钢配比高,加入增碳剂多的情况下,加入增碳剂要更加注意。
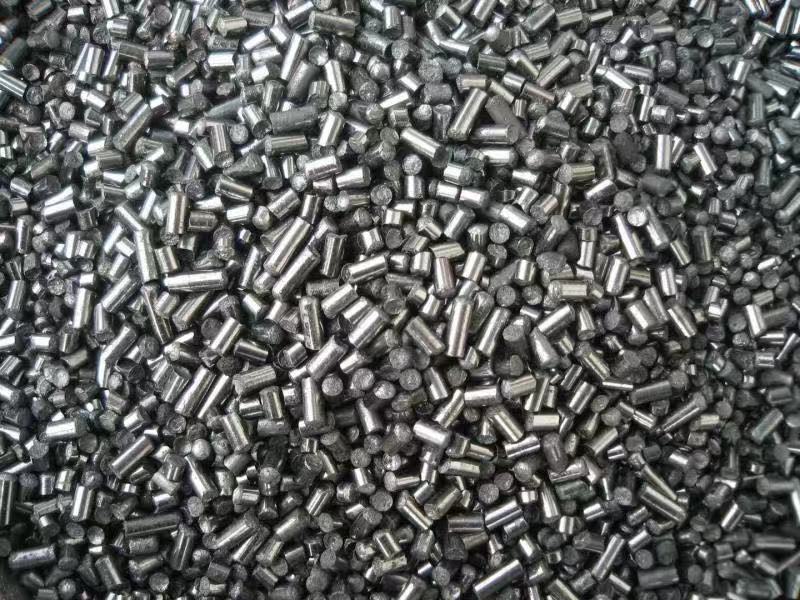
⑵提高原铁液的硅量,控制孕育量。
灰铸铁中的硅一部分是原铁液中的硅,一部分是孕育带入的硅。
许多人喜欢原铁液中的硅低点,然后用很大的孕育量孕育,这种做法并不科学:大量的孕育是不可取的,这会收缩倾向。孕育是为了增加结晶核心的数量,促进石墨化,少量的孕育(0.2%~0.4%)就可以达到这个目的。从工艺控制来说,孕育量应该相应稳定,不能有过大的变化。这就要求原铁液的硅量也要相应稳定。提高原铁液的硅量,既可以减少白口和收缩倾向,又能发挥硅固溶强化基体的作用,性能反而不降低。目前比较科学的做法是提高灰铸铁原铁液的含硅量,孕育量控制在0.3%左右,这样可以发挥硅的固溶强化作用,对提高强度有利,也对减少铸件收缩有利 。
⑶合金化的方法对铁液收缩有很大影响。
合金化能有效提高铸铁的性能,我们常用的合金元素是铬、钼、铜、锡、镍。
铬:铬能有效地提高灰铸铁的性能,随着加入量的增加,性能会一直提高。铬的白口倾向比较大,这是大家顾忌的问题。加入量太大,会出现碳化物。至于铬量的上限如何控制,不同的加铬工艺,上限有所不同,如果铬加入到原铁液中,其上限不要超过0.35%,提高原铁液中的铬量会使铁液白口倾向和收缩倾向加大,非常有害。
另一种加铬的工艺不是提高原铁液铬,而是将铬加入到铁液包中,用冲入法冲入,这种工艺会大大减少铁液的白口和收缩倾向,同前一种工艺相比,同样的铬量,白口和收缩倾向会减少一半以上,这种加铬方式,铬的上限可以控制到0.45%。
钼:钼的特性与铬非常相似。由于钼的价格昂贵,加钼会大幅度增加成本。因此,应尽可能少加钼,多加一些铬。用冲入法加铬、加钼是减少合金化收缩的有效措施。
⑷铁液浇注温度对收缩的影响。
温度高铁液收缩倾向大,这是大家都有的经验。要控制浇注温度在合理的范围内是非常重要的,浇注温度如果高于工艺规定的合理的温度20~30℃,收缩倾向就会大幅增加。生产中要注意这样一种现象,没有自动保温功能的电炉,可能会使铁液温度升高,包铁液的浇注温度会低一些,随后温度会越来越高,如果不加以控制,就有可能产生收缩废品。生产中包铁液要烫包,烫好的包再用,而且包铁液浇注温度要控制在下限,不要在上限,防止温度不断升高。电炉熔炼控制好浇注温度,是防止铸件产生收缩废品的关键措施。
⑸铁液氧化倾向不容忽略:氧化大、收缩大。
铁液氧化倾向大是非常有害的,也会收缩倾向。为了降低铁液氧化,冲天炉熔炼就要实现快速熔炼。现在国外的电炉熔炼技术可以做到加入的铁料在几分钟内快速熔化,大大缩短了铁料在高温氧化阶段的时间,氧化倾向大幅降低,同时由于电炉增碳技术的应用,使铁液的氧化进一步降低,所以电炉熔炼也可以生产出低氧化、低收缩的铁液。只要严格控制好浇注温度,用电炉熔炼生产复杂的缸体、缸盖铸件也很有优势。
m.trts0901.b2b168.com
电炉熔炼:增碳技术的应用是解决铁液收缩的关键技术。由于铁液凝固过程中的石墨析出产生石墨化膨胀作用,良好的石墨化会减少铁液的收缩倾向,因此,增碳技术是好的工艺。
由于加入增碳剂提高了铁液的石墨化能力,因此,采用全废钢熔炼加增碳剂的工艺,铁液的收缩倾向反而更小。这是非常重要的一个观念转变,传统的观念是认为多加废钢会铁液的收缩倾向,这样我们就容易走入一个误区,不愿意多用废钢,而喜欢多用一些生铁。
多用生铁的缺点是:生铁中有许多粗大的过共晶石墨,这种粗大的石墨具有遗传性,如果低温熔炼,粗大的石墨难以消除,粗大的石墨从液态遗传到了固态,使凝固过程中本来由于石墨析出应该产生的膨胀作用削弱,因此使铁液凝固过程中的收缩倾向,粗大的石墨又必然降低了材料的性能。因此,与用废钢增碳工艺相比,大量用生铁的缺点就是:①强度性能低。同样成分做过对比试验,性能低半个排号。②收缩倾向大。同样条件下,比废钢增碳工艺收缩大。
对于电炉熔炼,增碳技术的核心是使用的增碳剂。采用废钢增碳工艺,增碳剂就成为增碳工艺中重要的环节。增碳剂质量的好坏决定了铁液质量的好坏,增碳工艺能否获得好的石墨化效果,减少铁液收缩,主要取决于增碳剂:① 增碳剂一定要选用经过高温石墨化处理的增碳剂。只有经过高温石墨化处理,碳原子才能从原来的无序排列变成片状排列,片状石墨才能成为石墨形核的好核心,促进石墨化。②好的增碳剂含硫都非常低,w(S)小于0.03%是一个重要的指标。
对于冲天炉熔炼:高温熔炼是关键的技术指标,高温熔炼可以有效消除生铁粗大石墨的遗传性。高温熔炼可以提高渗碳率,减少配料中的生铁加入量。以渗碳方式获得的碳活性好,要比多加生铁带来的碳有更好的石墨化作用,反映在铸件上,就是石墨的形态更好,分布更均匀。石墨的形态好,就会提高材料的性能,包括切削性能,而 石墨化效果好,就能减少铁液的收缩倾向。
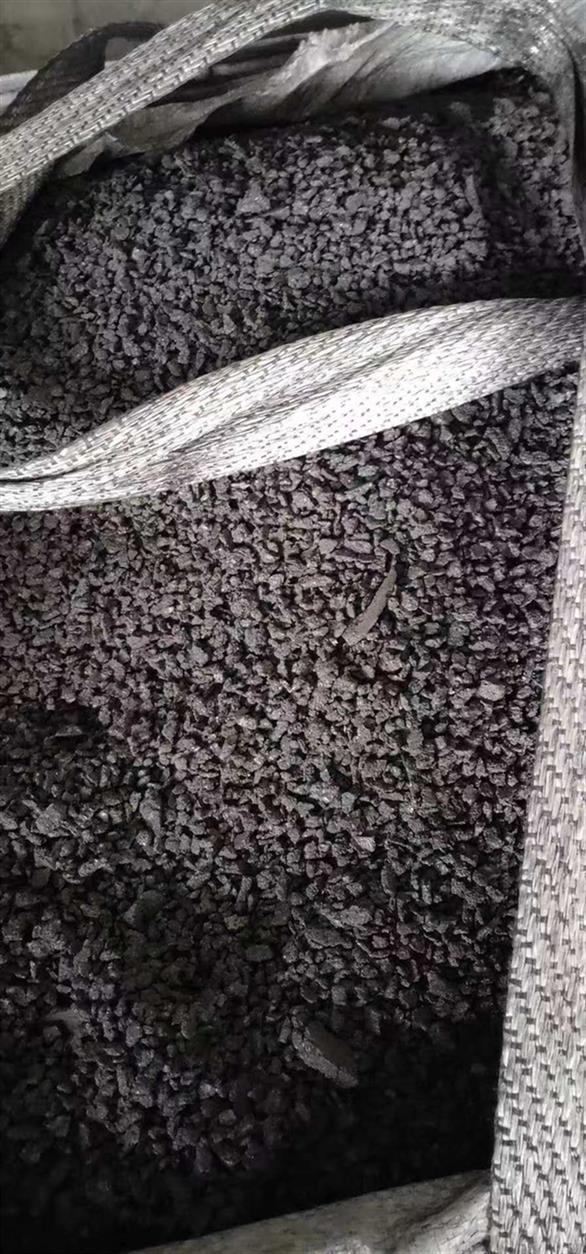
我厂下辖临漳县石峰碳素有限公司和临漳县和峰碳素经销处两家子公司。我厂碳素生产设备完善,技术力量雄厚,检测手段完善,产品质量上乘,品种齐全,主要产品有普通功率石墨电极,高功率石墨电极,特种石墨制品及新型碳素材料等。
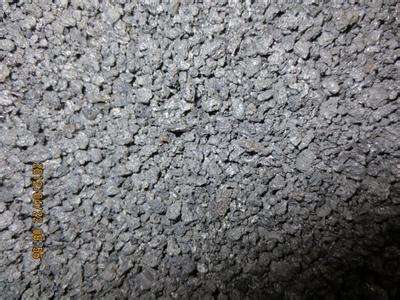
3、铁液化学成分对增碳剂增碳效果的影响
3.1硅对增碳剂增碳效果的影响
铁液中的硅对增碳效果有较大的影响。硅含量高的铁液增碳性不好。有人让铁液中Si的质量分数在0.6%~2.1%的范围内变化,并添加如表1所示的A,B两种增碳剂,观察加入增碳剂后增碳时间的区别,铁液中Si的质量分数高时,增碳速度慢。
3.2硫对增碳剂增碳效果的影响
正如铁液中的硅的质量分数对增碳效果的影响那样,硫的含量对增碳也有一定的影响。用表2中的A增碳剂,在添加前先加入试剂用的硫化铁,观察S的质量分数对增碳的影响。当添加硫化铁、铁液中S的质量分数为0.045%时,将它与无添加硫化铁、铁液中S的质量分数为0.0014%的低硫铁液相比较,增碳速度要迟缓得多。
4、增碳剂选择及加入方法
4.1应选择含氮量少的增碳剂
铸铁铁液中通常的氮的质量分数在100 ppm以下。如果含氮量超过此浓度(150-200 ppm或者更高),易使铸件产生龟裂、缩松或疏松缺陷,厚壁铸件更容易产生。这是由于废钢配比增加时,要加大增碳剂的加入量引起的。焦炭系增碳剂,特别是沥青焦含有大量的氮。电极石墨的氮的质量分数在0.1%以下或极微量,而沥青焦氮的质量分数约为0.6%。如果加入质量分数为0.6%氮的增碳剂2%,仅此就增加了120 ppm质量分数的氮。多量的氮不仅容易产生铸造缺陷,而且氮可以促使珠光体致密、铁素体硬化,强烈提高强度。
4.2增碳剂的加入方法
铁液的搅拌可以促进增碳,因此搅拌力弱的中频感应电炉与搅拌力强的工频感应电炉比较,增碳相对困难得多,所以中频感应电炉有增碳跟不上金属炉料的熔解速度的可能性。
即使是搅拌力强的工频感应电炉,增碳操作也不能忽视。这是因为,从感应电炉熔炼的原理图可知,感应电炉内存在开的搅拌铁流,在其边界的炉壁附近还存在着死角。在炉壁停留、附着的石墨团如果不用过度升温和长时间的铁液保温是不能熔入铁液的。铁液过度升温和长时间的保温,会铁液过冷度,有加大铸铁白口化的倾向。此外,对于在炉壁附近产生强感应电流的中频感应电炉来说,如果附着在炉壁的石墨团之间钻进铁液,在进行下一炉熔炼时,钻进的金属被熔化,导致侵蚀和损伤炉壁。因此,在废钢配比高,加入增碳剂多的情况下,加入增碳剂要更加注意。
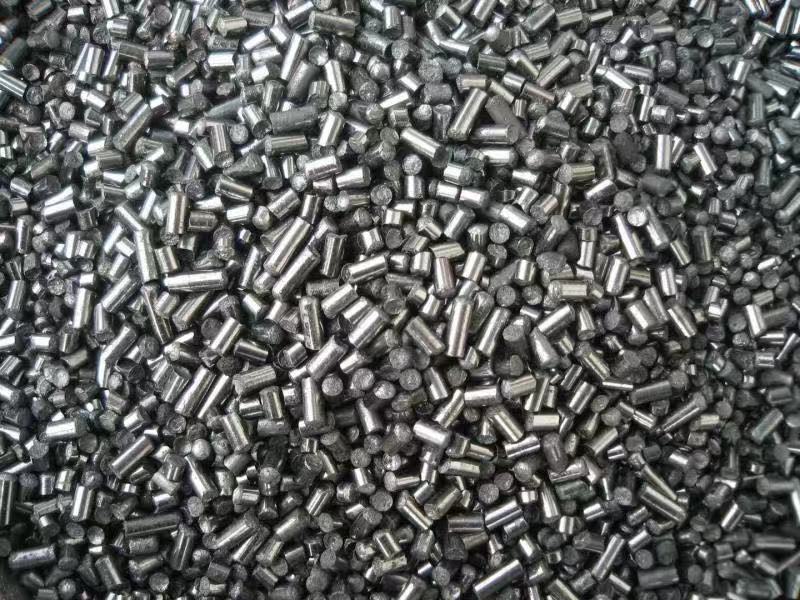
⑵提高原铁液的硅量,控制孕育量。
灰铸铁中的硅一部分是原铁液中的硅,一部分是孕育带入的硅。
许多人喜欢原铁液中的硅低点,然后用很大的孕育量孕育,这种做法并不科学:大量的孕育是不可取的,这会收缩倾向。孕育是为了增加结晶核心的数量,促进石墨化,少量的孕育(0.2%~0.4%)就可以达到这个目的。从工艺控制来说,孕育量应该相应稳定,不能有过大的变化。这就要求原铁液的硅量也要相应稳定。提高原铁液的硅量,既可以减少白口和收缩倾向,又能发挥硅固溶强化基体的作用,性能反而不降低。目前比较科学的做法是提高灰铸铁原铁液的含硅量,孕育量控制在0.3%左右,这样可以发挥硅的固溶强化作用,对提高强度有利,也对减少铸件收缩有利 。
⑶合金化的方法对铁液收缩有很大影响。
合金化能有效提高铸铁的性能,我们常用的合金元素是铬、钼、铜、锡、镍。
铬:铬能有效地提高灰铸铁的性能,随着加入量的增加,性能会一直提高。铬的白口倾向比较大,这是大家顾忌的问题。加入量太大,会出现碳化物。至于铬量的上限如何控制,不同的加铬工艺,上限有所不同,如果铬加入到原铁液中,其上限不要超过0.35%,提高原铁液中的铬量会使铁液白口倾向和收缩倾向加大,非常有害。
另一种加铬的工艺不是提高原铁液铬,而是将铬加入到铁液包中,用冲入法冲入,这种工艺会大大减少铁液的白口和收缩倾向,同前一种工艺相比,同样的铬量,白口和收缩倾向会减少一半以上,这种加铬方式,铬的上限可以控制到0.45%。
钼:钼的特性与铬非常相似。由于钼的价格昂贵,加钼会大幅度增加成本。因此,应尽可能少加钼,多加一些铬。用冲入法加铬、加钼是减少合金化收缩的有效措施。
⑷铁液浇注温度对收缩的影响。
温度高铁液收缩倾向大,这是大家都有的经验。要控制浇注温度在合理的范围内是非常重要的,浇注温度如果高于工艺规定的合理的温度20~30℃,收缩倾向就会大幅增加。生产中要注意这样一种现象,没有自动保温功能的电炉,可能会使铁液温度升高,包铁液的浇注温度会低一些,随后温度会越来越高,如果不加以控制,就有可能产生收缩废品。生产中包铁液要烫包,烫好的包再用,而且包铁液浇注温度要控制在下限,不要在上限,防止温度不断升高。电炉熔炼控制好浇注温度,是防止铸件产生收缩废品的关键措施。
⑸铁液氧化倾向不容忽略:氧化大、收缩大。
铁液氧化倾向大是非常有害的,也会收缩倾向。为了降低铁液氧化,冲天炉熔炼就要实现快速熔炼。现在国外的电炉熔炼技术可以做到加入的铁料在几分钟内快速熔化,大大缩短了铁料在高温氧化阶段的时间,氧化倾向大幅降低,同时由于电炉增碳技术的应用,使铁液的氧化进一步降低,所以电炉熔炼也可以生产出低氧化、低收缩的铁液。只要严格控制好浇注温度,用电炉熔炼生产复杂的缸体、缸盖铸件也很有优势。
m.trts0901.b2b168.com