东营石墨增碳剂厂家 青岛腾瑞炭素有限公司
浏览次数:243次
- 产品规格:
- 发货地:河北省邯郸临漳县
关键词
东营石墨增碳剂厂家
详细说明
⑵提高原铁液的硅量,控制孕育量。
灰铸铁中的硅一部分是原铁液中的硅,一部分是孕育带入的硅。
许多人喜欢原铁液中的硅低点,然后用很大的孕育量孕育,这种做法并不科学:大量的孕育是不可取的,这会收缩倾向。孕育是为了增加结晶核心的数量,促进石墨化,少量的孕育(0.2%~0.4%)就可以达到这个目的。从工艺控制来说,孕育量应该相应稳定,不能有过大的变化。这就要求原铁液的硅量也要相应稳定。提高原铁液的硅量,既可以减少白口和收缩倾向,又能发挥硅固溶强化基体的作用,性能反而不降低。目前比较科学的做法是提高灰铸铁原铁液的含硅量,孕育量控制在0.3%左右,这样可以发挥硅的固溶强化作用,对提高强度有利,也对减少铸件收缩有利 。
⑶合金化的方法对铁液收缩有很大影响。
合金化能有效提高铸铁的性能,我们常用的合金元素是铬、钼、铜、锡、镍。
铬:铬能有效地提高灰铸铁的性能,随着加入量的增加,性能会一直提高。铬的白口倾向比较大,这是大家顾忌的问题。加入量太大,会出现碳化物。至于铬量的上限如何控制,不同的加铬工艺,上限有所不同,如果铬加入到原铁液中,其上限不要超过0.35%,提高原铁液中的铬量会使铁液白口倾向和收缩倾向加大,非常有害。
另一种加铬的工艺不是提高原铁液铬,而是将铬加入到铁液包中,用冲入法冲入,这种工艺会大大减少铁液的白口和收缩倾向,同前一种工艺相比,同样的铬量,白口和收缩倾向会减少一半以上,这种加铬方式,铬的上限可以控制到0.45%。
钼:钼的特性与铬非常相似。由于钼的价格昂贵,加钼会大幅度增加成本。因此,应尽可能少加钼,多加一些铬。用冲入法加铬、加钼是减少合金化收缩的有效措施。
⑷铁液浇注温度对收缩的影响。
温度高铁液收缩倾向大,这是大家都有的经验。要控制浇注温度在合理的范围内是非常重要的,浇注温度如果高于工艺规定的合理的温度20~30℃,收缩倾向就会大幅增加。生产中要注意这样一种现象,没有自动保温功能的电炉,可能会使铁液温度升高,包铁液的浇注温度会低一些,随后温度会越来越高,如果不加以控制,就有可能产生收缩废品。生产中包铁液要烫包,烫好的包再用,而且包铁液浇注温度要控制在下限,不要在上限,防止温度不断升高。电炉熔炼控制好浇注温度,是防止铸件产生收缩废品的关键措施。
⑸铁液氧化倾向不容忽略:氧化大、收缩大。
铁液氧化倾向大是非常有害的,也会收缩倾向。为了降低铁液氧化,冲天炉熔炼就要实现快速熔炼。现在国外的电炉熔炼技术可以做到加入的铁料在几分钟内快速熔化,大大缩短了铁料在高温氧化阶段的时间,氧化倾向大幅降低,同时由于电炉增碳技术的应用,使铁液的氧化进一步降低,所以电炉熔炼也可以生产出低氧化、低收缩的铁液。只要严格控制好浇注温度,用电炉熔炼生产复杂的缸体、缸盖铸件也很有优势。
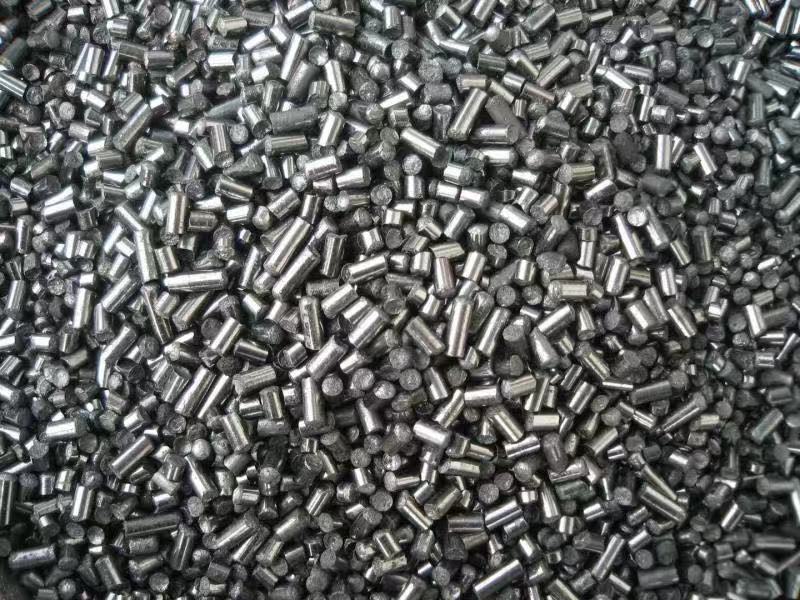
晶体石墨增碳剂的新用途:在生产高韧性风电球铁铸件、奥贝球铁铸件及大型复杂球铁柴油机缸体、缸盖过程中,经常遇到球化分级比2级低又比3级高,石墨球不圆整,石墨球直径达不到6级以上,EPC生产灰铸铁重卡变速机箱体出现了D型石墨等,采取了常规的工艺措施都难以解决问题,在生产原来配料、熔化、球化、孕育工艺不进行大的改变情况下,出铁时按1.5-2.0Kg/t铁液包中冲入0.5~1.0mm的晶体增碳剂(覆盖在球化剂上),这些问题就得到解决。换句话可以理解运用特定晶体增碳剂会对提高高韧性球铁风电铸件、奥贝球铁铸件、及大型复杂球铁柴油机缸体、缸盖的球化率、改善石墨球圆整度,减小石墨球直径起到有益的作用,EPC生产重卡变速机灰铸铁箱体对消除D型石墨有明显的效果。
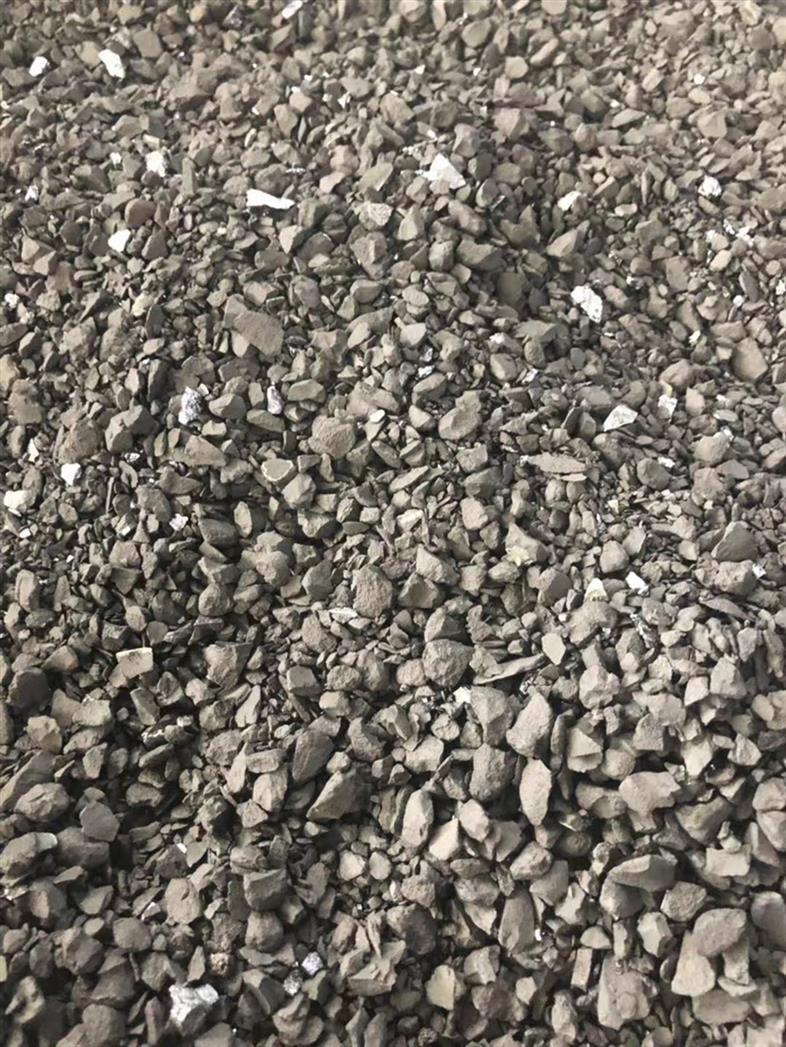
石墨电极主要以石油焦、针状焦为原料,煤沥青做结合剂,经煅烧、配料、混捏、压型、焙烧、石墨化、机加工而制成,是在电弧炉中以电弧形式释放电能对炉料进行加热熔化的导体,根据其质量指标高低,可分为普通功率石墨电极、高功率石墨电极和超高功率石墨电极。
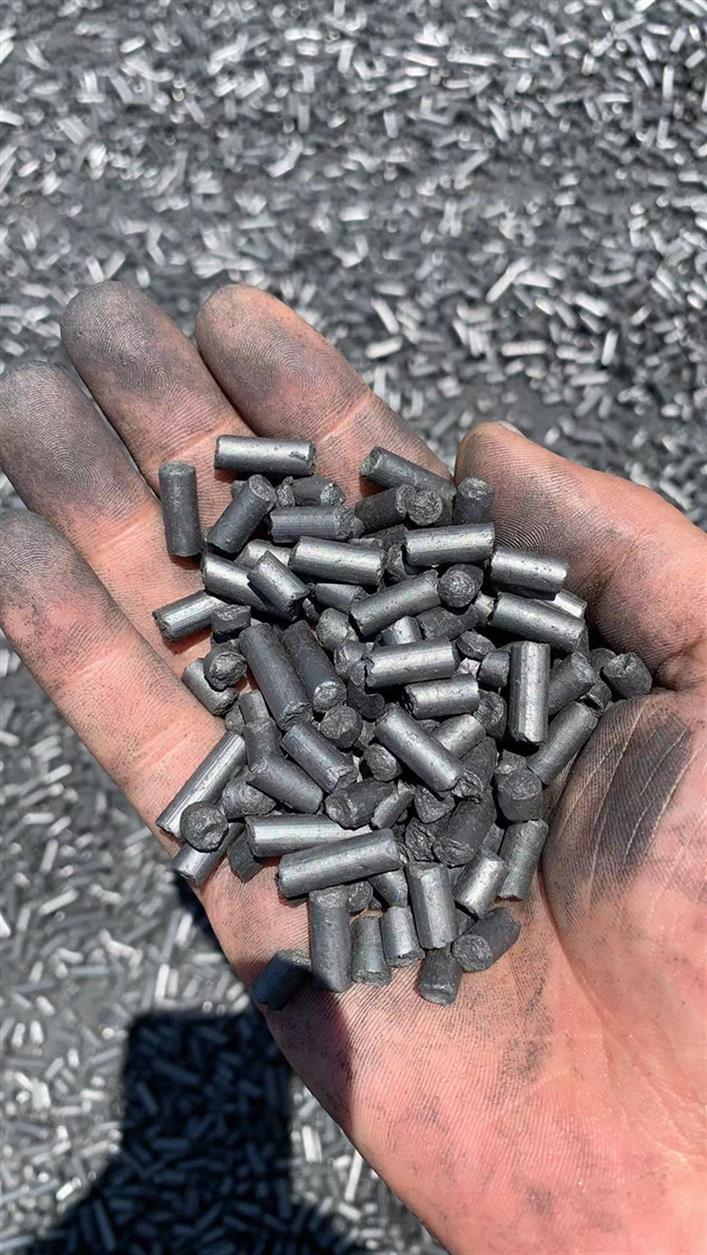
近年来,感应电炉用于熔炼铸铁已越来越多。通常,在感应电炉内仅靠加入金属炉料是不能确保铁液所需碳量的,必须补加增碳剂。为此,对于感应电炉,特别是中频感应电炉,添加增碳剂是熔炼操作的重要环节。今天就跟大家分享一下感应电炉熔炼铸铁,使用增碳剂应该注意哪些问题!
1、增碳剂中未熔解微粒的石墨化作用
在熔化的铁液中,增碳剂除了有已溶入铁液的碳以外,还有残留的、未溶入的石墨形式的碳,并以粒状被卷入搅拌的液流之中。未熔解、粗大的石墨粒子,在通电时大部分悬浮在炉壁附近的铁液液面,一部分则附着在相当于搅拌死角的炉壁中部。此时,一旦通电停止,这些粗大的石墨粒子由于浮力,会被缓缓地悬浮出来。超出光学显微镜所能观察范围的极微小的粒子在石墨熔解的过程中,不但在通电时,即使在通电停止时都能悬浮在铁液之中。
据介绍,越是接近于构成共晶晶核的物质,即使所添加的石墨与共晶石墨的结晶度有些不同,与其他能够推断为形成石墨核心的物质相比较,势必祸合度要大些。从此观点出发,可以认为:悬浮的微细石墨粒子有利于生成石墨核心,可起到防止铸铁过冷和白口化的作用。
2、增碳剂粒度对增碳效果的影响
2.1增碳剂粒度对增碳时间的影响
增碳剂粒度是影响增碳剂熔入铁液的主要因素。用表1中成分大致相同而粒度有所不同的A,B,C增碳剂作增碳效果试验,其结果如图1所示。尽管经过15min后的增碳率是相同的,但达到90%增碳率的增碳时间则大有区别。使用未经粒度处理的C增碳剂要13min,除去微粉的A增碳剂要8 min,而除去微粉和粗粒的B增碳剂仅需6min。这说明增碳剂的粒度对增碳时间有较大的影响,混入微粉和粗粒都不好,尤其在微粉含量高时。
2.2增碳剂粒度对增碳剂的影响
日本的中江和望月两人,曾对于质量分数99.8%的C和质量分数0.023%的S,粒度分布如表2的增碳剂作过增碳量的试验,试验结果如图2所示。从图中可以看出,粒度偏于微粉的增碳剂E的增碳效果极差,粒度偏于粗的增碳剂G的增碳效果较好;而适当除去微粉和粗粒的增碳剂A的增碳效果好。
以上事实证实,为了提高增碳效果,对增碳剂应作除去微粉和粗粒的粒度处理。
m.trts0901.b2b168.com
灰铸铁中的硅一部分是原铁液中的硅,一部分是孕育带入的硅。
许多人喜欢原铁液中的硅低点,然后用很大的孕育量孕育,这种做法并不科学:大量的孕育是不可取的,这会收缩倾向。孕育是为了增加结晶核心的数量,促进石墨化,少量的孕育(0.2%~0.4%)就可以达到这个目的。从工艺控制来说,孕育量应该相应稳定,不能有过大的变化。这就要求原铁液的硅量也要相应稳定。提高原铁液的硅量,既可以减少白口和收缩倾向,又能发挥硅固溶强化基体的作用,性能反而不降低。目前比较科学的做法是提高灰铸铁原铁液的含硅量,孕育量控制在0.3%左右,这样可以发挥硅的固溶强化作用,对提高强度有利,也对减少铸件收缩有利 。
⑶合金化的方法对铁液收缩有很大影响。
合金化能有效提高铸铁的性能,我们常用的合金元素是铬、钼、铜、锡、镍。
铬:铬能有效地提高灰铸铁的性能,随着加入量的增加,性能会一直提高。铬的白口倾向比较大,这是大家顾忌的问题。加入量太大,会出现碳化物。至于铬量的上限如何控制,不同的加铬工艺,上限有所不同,如果铬加入到原铁液中,其上限不要超过0.35%,提高原铁液中的铬量会使铁液白口倾向和收缩倾向加大,非常有害。
另一种加铬的工艺不是提高原铁液铬,而是将铬加入到铁液包中,用冲入法冲入,这种工艺会大大减少铁液的白口和收缩倾向,同前一种工艺相比,同样的铬量,白口和收缩倾向会减少一半以上,这种加铬方式,铬的上限可以控制到0.45%。
钼:钼的特性与铬非常相似。由于钼的价格昂贵,加钼会大幅度增加成本。因此,应尽可能少加钼,多加一些铬。用冲入法加铬、加钼是减少合金化收缩的有效措施。
⑷铁液浇注温度对收缩的影响。
温度高铁液收缩倾向大,这是大家都有的经验。要控制浇注温度在合理的范围内是非常重要的,浇注温度如果高于工艺规定的合理的温度20~30℃,收缩倾向就会大幅增加。生产中要注意这样一种现象,没有自动保温功能的电炉,可能会使铁液温度升高,包铁液的浇注温度会低一些,随后温度会越来越高,如果不加以控制,就有可能产生收缩废品。生产中包铁液要烫包,烫好的包再用,而且包铁液浇注温度要控制在下限,不要在上限,防止温度不断升高。电炉熔炼控制好浇注温度,是防止铸件产生收缩废品的关键措施。
⑸铁液氧化倾向不容忽略:氧化大、收缩大。
铁液氧化倾向大是非常有害的,也会收缩倾向。为了降低铁液氧化,冲天炉熔炼就要实现快速熔炼。现在国外的电炉熔炼技术可以做到加入的铁料在几分钟内快速熔化,大大缩短了铁料在高温氧化阶段的时间,氧化倾向大幅降低,同时由于电炉增碳技术的应用,使铁液的氧化进一步降低,所以电炉熔炼也可以生产出低氧化、低收缩的铁液。只要严格控制好浇注温度,用电炉熔炼生产复杂的缸体、缸盖铸件也很有优势。
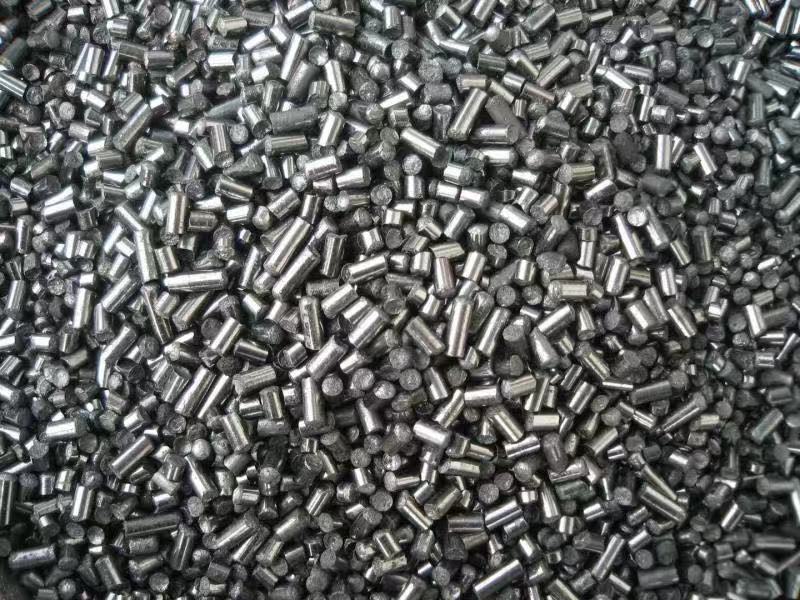
晶体石墨增碳剂的新用途:在生产高韧性风电球铁铸件、奥贝球铁铸件及大型复杂球铁柴油机缸体、缸盖过程中,经常遇到球化分级比2级低又比3级高,石墨球不圆整,石墨球直径达不到6级以上,EPC生产灰铸铁重卡变速机箱体出现了D型石墨等,采取了常规的工艺措施都难以解决问题,在生产原来配料、熔化、球化、孕育工艺不进行大的改变情况下,出铁时按1.5-2.0Kg/t铁液包中冲入0.5~1.0mm的晶体增碳剂(覆盖在球化剂上),这些问题就得到解决。换句话可以理解运用特定晶体增碳剂会对提高高韧性球铁风电铸件、奥贝球铁铸件、及大型复杂球铁柴油机缸体、缸盖的球化率、改善石墨球圆整度,减小石墨球直径起到有益的作用,EPC生产重卡变速机灰铸铁箱体对消除D型石墨有明显的效果。
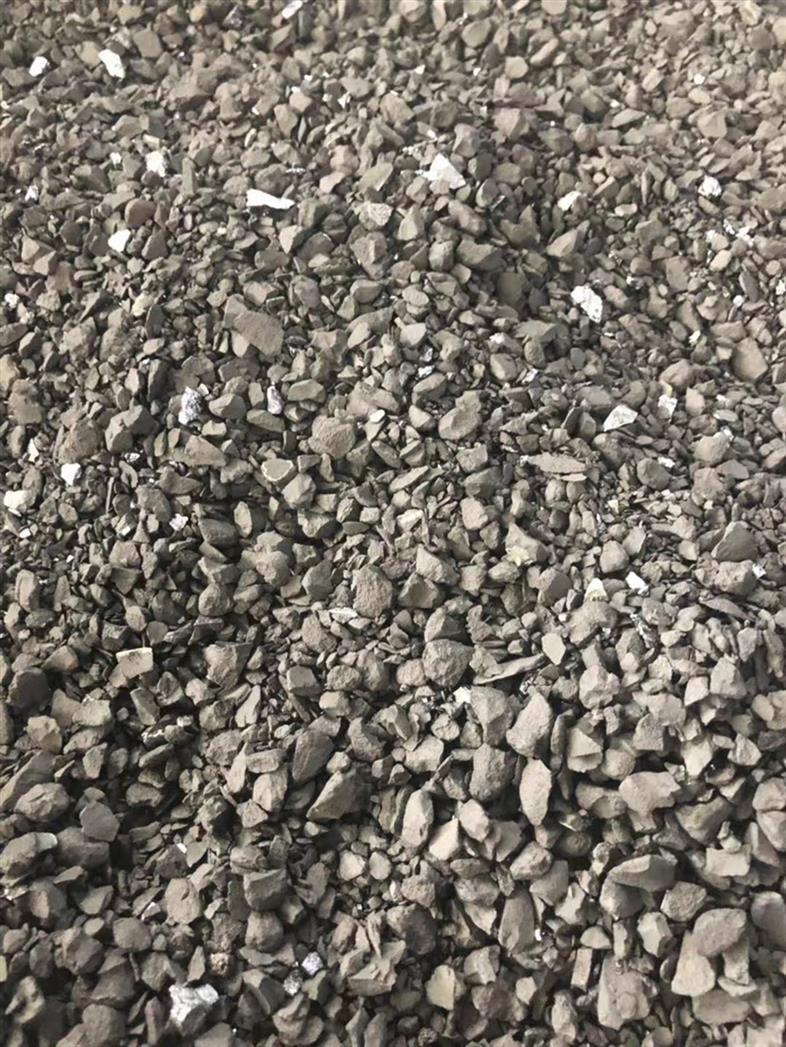
石墨电极主要以石油焦、针状焦为原料,煤沥青做结合剂,经煅烧、配料、混捏、压型、焙烧、石墨化、机加工而制成,是在电弧炉中以电弧形式释放电能对炉料进行加热熔化的导体,根据其质量指标高低,可分为普通功率石墨电极、高功率石墨电极和超高功率石墨电极。
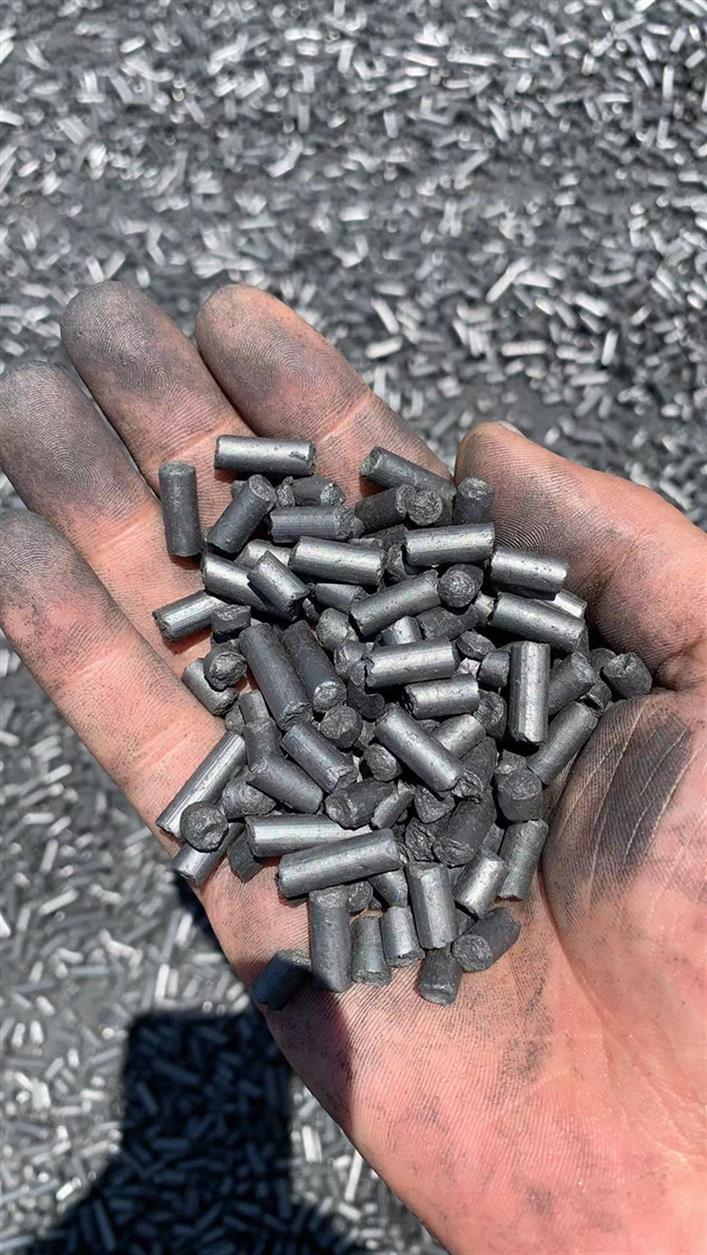
近年来,感应电炉用于熔炼铸铁已越来越多。通常,在感应电炉内仅靠加入金属炉料是不能确保铁液所需碳量的,必须补加增碳剂。为此,对于感应电炉,特别是中频感应电炉,添加增碳剂是熔炼操作的重要环节。今天就跟大家分享一下感应电炉熔炼铸铁,使用增碳剂应该注意哪些问题!
1、增碳剂中未熔解微粒的石墨化作用
在熔化的铁液中,增碳剂除了有已溶入铁液的碳以外,还有残留的、未溶入的石墨形式的碳,并以粒状被卷入搅拌的液流之中。未熔解、粗大的石墨粒子,在通电时大部分悬浮在炉壁附近的铁液液面,一部分则附着在相当于搅拌死角的炉壁中部。此时,一旦通电停止,这些粗大的石墨粒子由于浮力,会被缓缓地悬浮出来。超出光学显微镜所能观察范围的极微小的粒子在石墨熔解的过程中,不但在通电时,即使在通电停止时都能悬浮在铁液之中。
据介绍,越是接近于构成共晶晶核的物质,即使所添加的石墨与共晶石墨的结晶度有些不同,与其他能够推断为形成石墨核心的物质相比较,势必祸合度要大些。从此观点出发,可以认为:悬浮的微细石墨粒子有利于生成石墨核心,可起到防止铸铁过冷和白口化的作用。
2、增碳剂粒度对增碳效果的影响
2.1增碳剂粒度对增碳时间的影响
增碳剂粒度是影响增碳剂熔入铁液的主要因素。用表1中成分大致相同而粒度有所不同的A,B,C增碳剂作增碳效果试验,其结果如图1所示。尽管经过15min后的增碳率是相同的,但达到90%增碳率的增碳时间则大有区别。使用未经粒度处理的C增碳剂要13min,除去微粉的A增碳剂要8 min,而除去微粉和粗粒的B增碳剂仅需6min。这说明增碳剂的粒度对增碳时间有较大的影响,混入微粉和粗粒都不好,尤其在微粉含量高时。
2.2增碳剂粒度对增碳剂的影响
日本的中江和望月两人,曾对于质量分数99.8%的C和质量分数0.023%的S,粒度分布如表2的增碳剂作过增碳量的试验,试验结果如图2所示。从图中可以看出,粒度偏于微粉的增碳剂E的增碳效果极差,粒度偏于粗的增碳剂G的增碳效果较好;而适当除去微粉和粗粒的增碳剂A的增碳效果好。
以上事实证实,为了提高增碳效果,对增碳剂应作除去微粉和粗粒的粒度处理。
m.trts0901.b2b168.com